Heat Treatment Consultancy
Heat Treatment Services
Leveraging our rich legacy of over 90 years in heat treatment practices, we transitioned our focus in 2022 to provide impartial, expert consultancy in this field. We are committed to sharing our extensive knowledge and proficiency to help you optimise your heat treatment processes, ensuring the highest levels of quality and efficiency in your operations.
Our Experience
With nine decades of hands-on experience in the field, our knowledge extends across a multitude of industries and heat treatment processes. From traditional annealing, hardening, and tempering to advanced processes like carburizing, nitriding, and induction heat treatment, our consultants have dealt with them all.
Our impartiality as consultants is underpinned by our extensive experience. We’ve worked with various materials and industries, ensuring our guidance is rooted in practical application and holistic understanding. Whether you’re a small-scale manufacturer or a global enterprise, we’re confident in our ability to contribute positively to your heat treatment operations.
Enlist Keighley Labs’ Heat Treatment Consultancy Services today to tap into our wealth of knowledge and experience. Let’s work together to optimise your heat treatment processes and boost your operational efficiency.
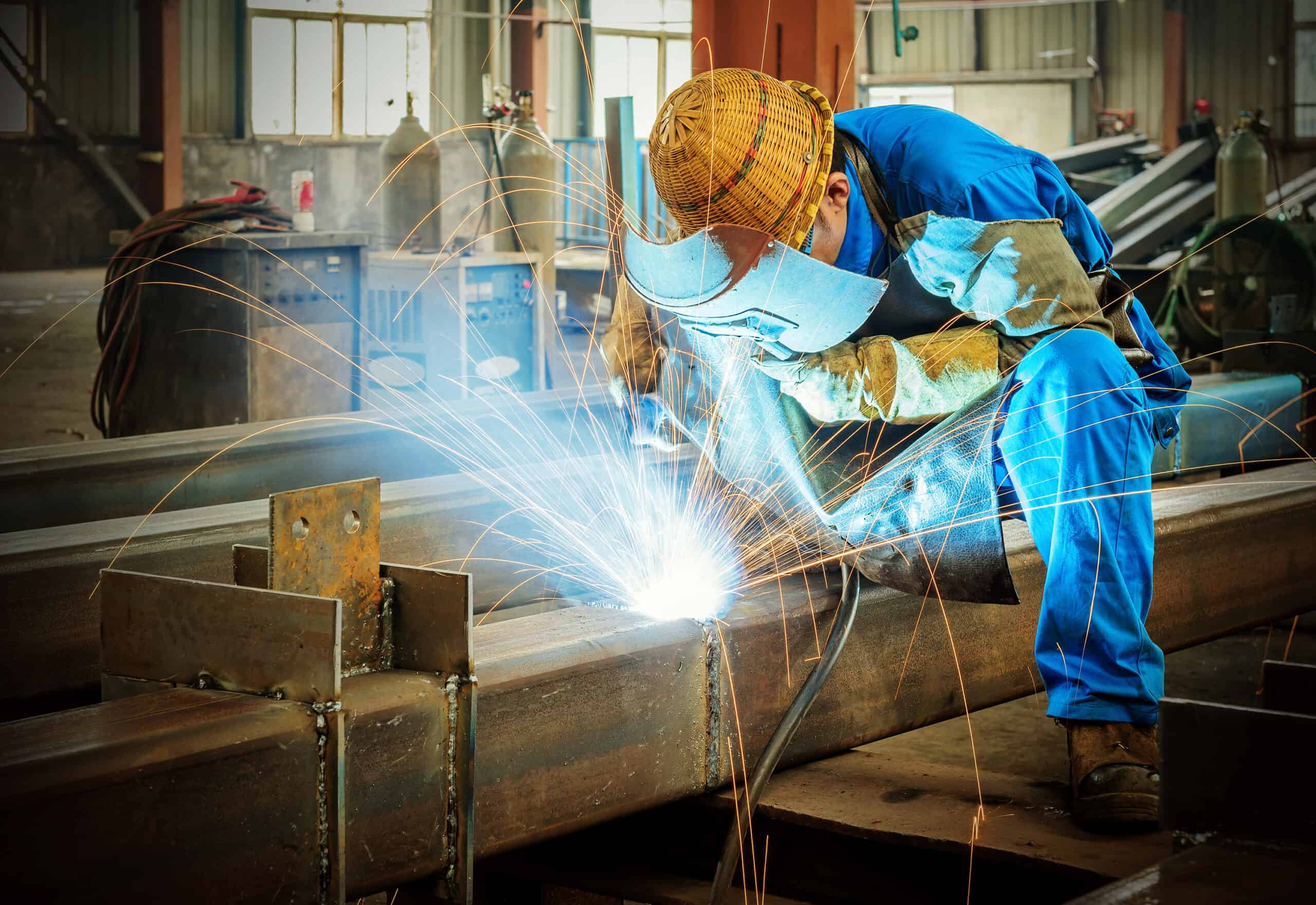
Our Solutions
We offer a comprehensive suite of solutions tailored to your unique needs, focused on enhancing your heat treatment process. Our consultants are equipped with decades of hands-on experience and technical acumen to provide valuable insights into your existing processes, identify potential areas for improvement, and recommend innovative solutions.
Our services encompass everything from process optimisation, failure analysis, and metallurgical investigations to understanding industry best practices and compliance with international standards.
Supporting Services
In addition to our core consultancy services, we offer supplementary support to ensure your heat treatment operations run smoothly. These include:
- Process Troubleshooting: We help identify and rectify technical challenges affecting your heat treatment processes.
- Training: We provide bespoke training for your team to enhance their understanding and operation of heat treatment processes.
- Quality Control: Our experts can guide you in setting up effective QC systems to ensure your heat treatment results are consistent and meet required specifications.
- Equipment Selection: We can assist in the selection of appropriate heat treatment equipment for your specific requirements, considering factors such as process efficiency, operational cost, and quality of output.
Types of Heat Treatment
At Keighley Labs, our expertise spans across a wide array of heat treatment processes. Here’s an overview of the types of heat treatments we have extensive experience in and regularly provide consultancy for:
Annealing: Our consultants can guide you on the best practices for annealing, a heat treatment process that alters the physical properties of a material to increase its ductility and reduce its hardness.
Hardening: We offer advice on hardening processes, which are aimed at increasing the hardness and strength of materials.
Tempering: Our team can provide valuable insights into tempering procedures, a process used to increase the toughness of iron-based alloys.
Carburizing: We’ve worked with numerous industries in providing consultation on carburizing, a heat treatment process that enriches the surface layer of low-carbon steel with carbon.
Nitriding: Our consultants have a wealth of experience in advising on nitriding, a heat treatment process that diffuses nitrogen into the surface of a metal to create a case-hardened surface.
Induction Heat Treatment: We can help optimize your induction heat treatment processes, which use induction heating to achieve the heat treatment effect.
Normalizing: Our consultants are experienced in advising on normalizing processes, which heat steel or iron above its critical temperature and allow it to cool in open air to room temperature to relieve internal stresses and reduce brittleness.
Quenching: We can provide guidance on quenching, a rapid cooling process used to increase the hardness of metal.
Case Hardening: Our team can provide insights into case hardening techniques, a process that hardens the surface of a metal by infusing elements into the material’s surface, forming a thin layer of a harder alloy.
Austempering: We offer advice on austempering, a heat treating process that creates a bainitic microstructure in steel and ductile iron to increase strength, toughness, and reduce distortion.
Martempering (Marquenching): Our consultants have experience advising on martempering, a form of isothermal heat treatment designed to reduce the rate of cooling and prevent the formation of unwanted phases.
Precipitation hardening (Age hardening): We provide consultancy on precipitation hardening, a heat treatment technique used to increase the yield strength of malleable materials, including most structural alloys of aluminium, magnesium, nickel, titanium, and some steels and stainless steels.
Stress Relieving: We advise on stress relieving treatments which are used to remove or reduce the internal stresses created in a metal due to the performance of cold working, heat treatment, or machining.
Solution Annealing (Solution Treatment): Our team can offer guidance on solution annealing processes, often used in the aerospace industry and for stainless steels and certain nickel alloys to promote corrosion resistance and to prepare the alloy for further hardening.