Non-Destructive Testing/Checks
Covering a wide range of testing techniques, Keighley Laboratories provide industry accredited Non-Destructive Testing processes used to evaluate the properties of a material, part, product, weld or system without causing any damage.Our team of experienced technicians work with a wide range of clients from different industries that require NDT/NDE requirements. These include companies in manufacturing, oil and gas, aerospace, public infrastructure, automotive and power generation industries.
NDT covers a wide range of different testing techniques and processes, offering services including liquid penetrative testing and inspection, magnetic particle inspection, ultrasonic flaw detection, positive material identification, magnetic permeability, conductivity, ferrite determination and portable hardness testing. The majority of tests can be carried out either in-house or at a customer’s premises.
Process
Liquid Penetrant Testing or Dye Penetrant Inspection (LPT, DPI or PT)
This process is used for the detection of surface-breaking discontinuities on magnetic and non-magnetic metallic materials.
Fluorescent and colour contrast penetrants are available to be used in the following methods:
- Water washable
- Solvent removable
Magnetic Particle Inspection (MPI/MT)
MPI/MT is used to detect surface breaking indications, and slight sub-surface discontinuities (up to 2mm). This is done primarily on ferromagnetic materials such as iron, nickel, cobalt and some of their alloys.
Bench type crack detectors and portable units are employed producing various waveforms (i.e. A.C, HWDC and induced magnetic flow), to give both circular and longitudinal magnetism.
On-site testing is also carried out using electromagnetic yokes and permanent magnets producing induced magnetic flow.
Ultrasonic Flaw Detection (UT)
This process, also known as Ultrasonic Inspection, is used for the detection of volumetric discontinuities in ferrous and non-ferrous products (forgings and castings etc.), and welds in magnetic and non-magnetic metals.
The process is capable of penetrating metals, dependent on the material characteristics, up to 10m in length.
Some thickness and depth checks can also be carried out using ultrasound.
Radiography
At Keighley Laboratories we are able to provide radiography services through sub-contract. These are booked in advance, and notice is required for on-site work.
Personnel
Our team of experienced and highly skilled technicians are available at short notice for any projects. This can be for in-house or on-site work in the UK and overseas.
All of our inspectors who undertake non-destructive testing are qualified to, and meet a minimum of PCN Level 2.
All of our technicians can assist clients in product qualification, material testing, quality assurance and audit programmes.
Ancillary non-destructive processes are available at Keighley Laboratories, click on the link for further details: additional NDT processes.
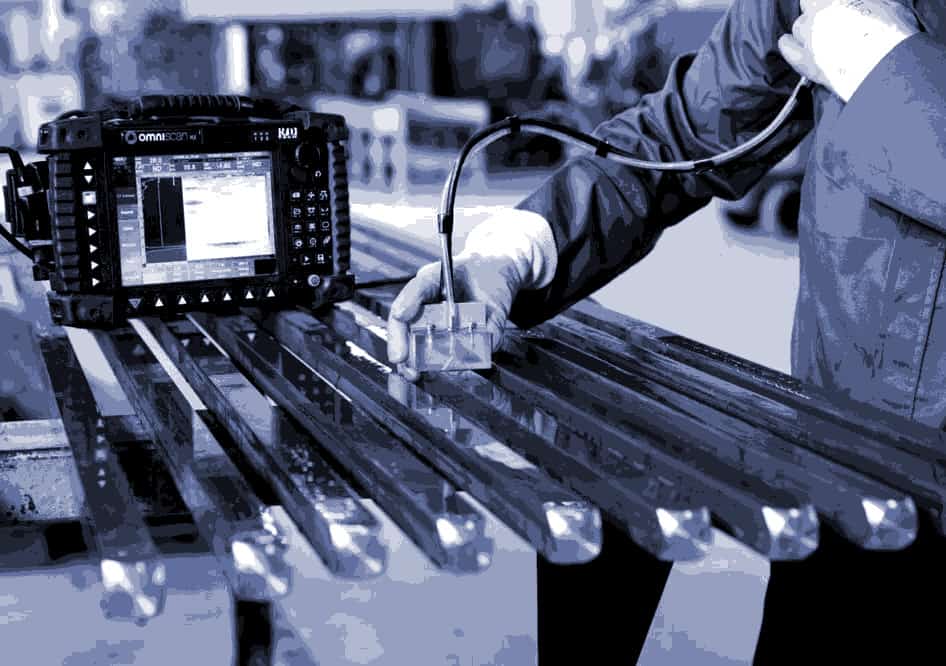
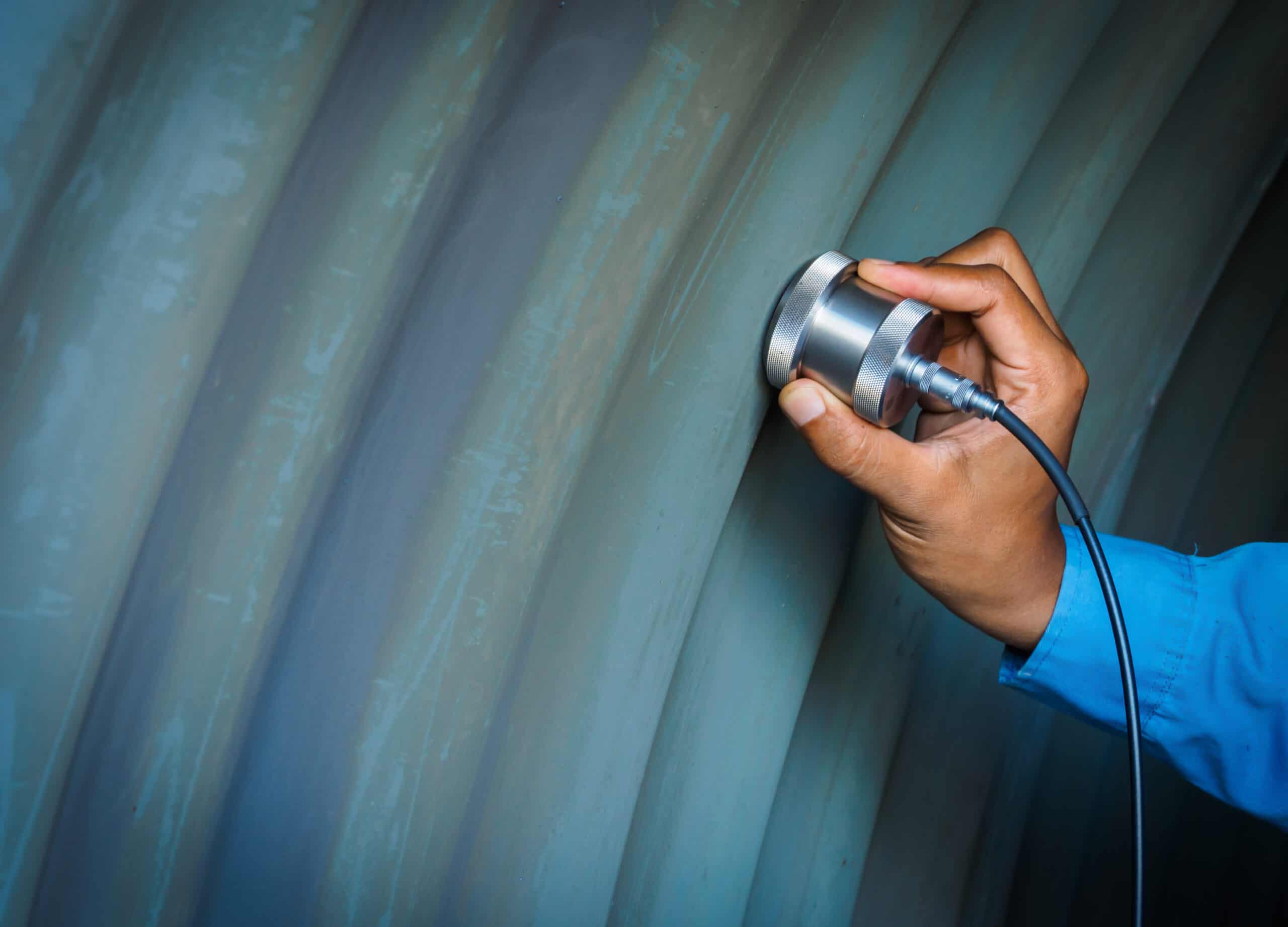
Benefits of Non-Destructive Testing
Non-destructive testing provides a wide range of benefits to companies and organisations with NDT requirements. Our services can help you identify defects that could prove to be disastrous, preventing future failures from occurring.
With all types of NDT, one of the primary benefits is that the product itself is not damaged, using reliable and repeatable methods of analysis.
The range of analytical methods means that the process can be tailored to your needs. The testing processes can be carried out on magnetic and non-magnetic materials. Additionally, the testing can be carried out on actual components or test samples, reducing waste and providing economical advantages over destructive testing and providing assurance of product integrity.
Technical Specifications
Liquid Penetrant Testing (LPT)
For special applications dual penetrants (fluorescent and colour contrast) can be obtained as can thixotropic penetrants (those with variable viscosity) for use on critical areas of on-site components. Testing can be undertaken both in-house and on-site, working to national and international specifications.
Magnetic Particle Inspection (MT/MPI)
Indications of discontinuities are revealed using fluorescent and colour contrast detecting media. Testing can be undertaken in-house or on-site, working to national and international specifications.
Ultrasonic Flaw Detection (UT)
Undertaken using digital and analogue machines capable of ‘A’ scan display at frequencies up to 6MHz employing both normal (0 degree) and angle probes. Ultrasonic flaw detection is capable of testing most metallic materials up to 10m in length, dependent on the material characteristics. Tests in-house or on-site, working to national and international specifications.
Matthew Mellor
Technical Services Director
General Enquiries
Test House Manager
Contact Us
Telephone No.+44 (0)1535 664211